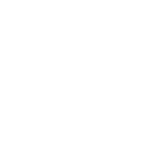
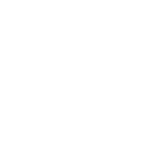
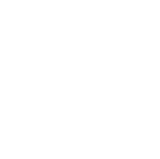
E_Engineering
An entire product family harmonised through a uniform design.
One-of-a-kind, premium electrosurgery handpieces with brand-neutral device connectors.
One-of-a-kind, premium electrosurgery handpieces with brand-neutral device connectors.
Monopolar electrode handpiece for high-frequency surgery
Our customers are as familiar with the benefits of high-frequency surgery as they are with the back of their hand. And know that the ergonomic benefits literally fit comfortably in the hand.
Uniform design, ergonomic grip and significantly optimised performance thanks to ‘Great Performance Engineering’ – covering the entire process from purchasing through development to manufacturing within the scope of a highly efficient production line concept, NICOLAY created a brand-neutral OEM device connector solution: electrode handpieces for high-frequency surgery that are biocompatible, compliant with all applicable standards, designed to meet voltage requirements of at least 10 kVp according to IEC 601, and ready for 350 preparation cycles. Available with one button, two buttons or a rocker for cut and coag – and even with clip-on fume extraction, if required. Good energy for healthy patients.
The task
Numerous manufacturers, numerous handpieces, numerous HF generators with a variety of device connectors. That was the starting point. The customer tasked us with replacing a large part of the existing electrosurgery handpieces for various manufacturers with a new handpiece with a standardised design. The objective was to develop an appealing design with improved ergonomics and feel for the new product family. These are handpieces with extremely sophisticated features – such as a version with power adjustment, designed for 350 instead of the usual 100 treatment cycles, and equipped with a higher power of 10 kVp. They needed to be surgical handpieces with detachable cables and brand-neutral device connectors – compatible with HF generators from various manufacturers. In other words, truly intelligent monopolar electrode handpieces – premium electrode handpieces. And intelligent is also the perfect way to describe the development and the production process.
The challenges
The challenge, first and foremost, was to develop approx. 20 different versions of the surgical handpieces designed to be connected to high-frequency surgical generators, which had to meet the safety requirements of DIN EN 60601-1 in general and, in particular, the requirements for the safety of high-frequency surgical equipment according to DIN EN 60601-2-2. The range of electrode diameters required was already quite extensive, ranging from 1.6 mm for dental applications to 2.4 mm and 4 mm for all electrodes commonly available on the market. In addition, there needed to be conventional versions with two buttons or with a rocker for cut and coag, as well as one each with a button, without a button and optionally with an additional rocker for power adjustment.
Furthermore, it needed to be possible to connect the handpieces to competitors’ generators. All in all, it was a matter of designing and manufacturing a total of four device connectors. RFID transponders for US 3-pole connectors also had to be taken into account. Another version called for handpieces compatible with separable and interchangeable connection cables.
The design of the handpieces had to allow for fume extraction, for example in a form that could be clipped onto the handpiece. At least one version had to meet increased voltage requirements of at least 10 kVp according to IEC 601. The handpieces were to be designed for 350 conventional steam sterilisation cycles up to 134 °C as well as Sterrad (plasma sterilisation) cycles. Finally, biocompatibility according to EN ISO 10993-1 (cytotoxicity and chem. characterisation), cleaning validation as well as a service life of three years all had to be guaranteed.
And all this needed to be achieved at explicitly specified target costs and annual quantities and in accordance with DIN EN 60601-2-2 (Safety and essential performance characteristics of high-frequency surgical equipment and HF accessories). In other words, this was no walk in the park.
The solution and the added value
Breaking new ground in purchasing and procurement
The customer’s price specifications alone precluded the purchase and procurement of, for example, stamped or metal parts as well as spring baskets to hold the electrodes or components of the device connectors from well-known European suppliers. Within a very short time, we searched for and found suitable suppliers around the world with the appropriate qualifications. But even here, realising the target prices was only possible by calculating with sizable purchase quantities. The solution here was a volume agreement with the suppliers.
GPE developed mechanical masterpieces
Since the customer did not specify which version needed to meet the increased voltage requirement in advance, we incorporated it into the design of every version. With injection moulds featuring a sophisticated design – perfectly tailored to the handle sleeve and the soft component – we succeeded in developing an ergonomically optimised curved design. With a keen eye for the essentials, GPE and the client agreed to design the spring assembly with a holding force that at least meets the standard – and how this should be tested. While the customer had defined the insertion and extraction force for the device connectors in advance, the device socket as an interface was still undefined, which meant that it was not yet possible to design the various connector geometries at that time. In this case, we here at NICOLAY conducted in-house development – working closely with the customer , of course, in order to find an OEM solution that could be used by all manufacturers. With a very simple but cleverly balanced cable construction, it was possible to both meet the stringent alternate bending tests and comply with the equally stringent price specifications.
Electrifying solutions found for high-voltage challenges
While conducting high-voltage electrical tests, we found that different frequencies sometimes caused the handpiece to heat up. At this point, we put the testing conditions to the test ourselves and ultimately solved the proof of dielectric strength with the customer’s generator. In the process, we tested all available parameters to ensure that the handpiece meets the required 10 kVp according to IEC 601-1/44.7.
Responding with flexibility to regulatory changes
If the rules change in the middle of the game, it takes flexibility and creativity to still score the point. In this case, it was regulatory changes that led to a cleaning validation towards the end of the project – and to a revision of the initially selected design of a closed housing. In this case, we found a solution which delivered results in the laboratory that satisfied all parties involved: subsequently added openings. The monopolar electrode handpieces even successfully withstood the required 350 sterilisation cycles in a test carried out by the customer themselves at their own premises. Biocompatibility was demonstrated through testing conducted using the finished handpiece. However, due to the open design of the handpiece, critical components could have been dissolved without patient contact, which would have led to a negative result. Through adapted, real-world testing conditions and taking risk management into account, this requirement was approved by the customer.
All ducks in a row, quickly and flexibly assembled
Our production-optimised line concept enabled the efficient assembly of all components into the housing parts – well-arranged, fast, flexible and cost-effective. The housing parts were sealed by means of soft overmoulding. It hides parting lines and prevents the possibility of disruptive discharge. This assembly concept could be realised by a sophisticated injection moulding tool concept. The pre-assembled unit and the soft overmoulding were harmonised with each other over several rounds.
The application
The result are premium surgical handpieces that offer truly unique selling points with their sterilisation cycles and power adjustment. With their unmistakable red and white design, they are representative of a standardised product range. It is a validated handpiece that complies with all currently applicable standards. All device connectors are proprietary NICOLAY developments and can be used by other customers. An intelligent electrode handpiece has been created in the truest sense of the word. Clever through and through – in all its components.